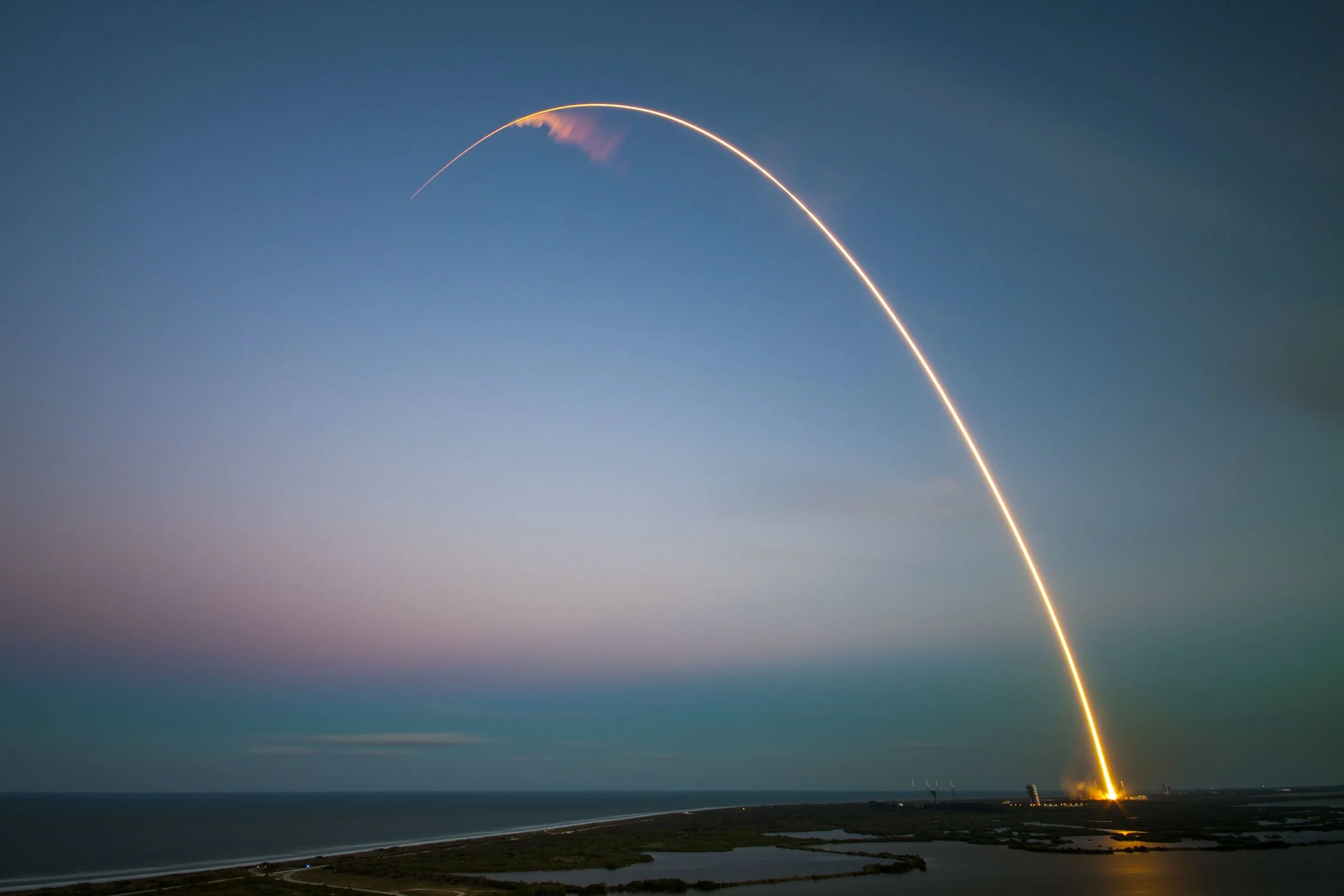
Aerospace
Using legacy measurement systems to make measurements on an aircraft structure may require literally hundreds of sensors, including single- and multi-axis accelerometers, strain gauges, LVDTs, and extensometers. Each of these must be attached to the aircraft structure at well-defined locations to obtain data, requiring both time and considerable care. Today, much of the legacy technology has been replaced by the stereo digital image correlation method originally developed and transitioned to industry by Correlated Solutions scientists and engineers. Using multiple stereo-vision systems provided by Correlated Solutions, images of an aircraft or aerospace component can be acquired as it is loaded and then analyzed using VIC-3D software to obtain the displacement and strain fields during mechanical testing. In addition, using the patented vibration analysis (FFT) software with images, full-field operational deflection shapes (ODSs) and vibrational frequencies also can be obtained by analyzing the images acquired during transient events.
Without question, the stereo DIC systems from Correlated Solutions are already reducing the required testing time for aerospace structures. In addition, DIC provides a rich set of data to improve understanding of structural deformations and structural dynamics and allows aerospace testing teams to be more efficient while also improving understanding of aerospace structures.
Application Examples
Mars Rover Heat Shield and Digital Image Correlation
In advance of the launching of the Mars 2020 Perseverance Rover, NASA deployed the VIC-3D Multi-System in the development of the heat shield – a crucial component for the Rover to enter the Martian atmosphere safely.
DIC for Understanding Weld & Base Metal Behavior
Engineers endeavored to understand the behavior of friction stir welds from the initial discovery of fracturing to tension and sheer testing using the VIC-2D system to explore how the production parameters impact the properties of the welded materials.
NASA 360° Buckling Test with Real-Time Module
Cylindrical rocket shells are subject to lifting loads referred to as a “Shell Buckling Knockdown Factor” or SBKF. The available technology for original SBKF models in the 1960’s limited the accuracy of these models. DIC changed all that.
Ultra-High-Speed, Super Dynamic Bend Test
VIC-3D combined with ultra-high-speed cameras generates extremely accurate full-field strain data helping validate theoretical models which are ultimately used to improve manufacturing efficiency without sacrificing safety and structural integrity.